Application of Rubber Melt Gear Pump in Rubber Processing
Rubber melt gear pump, as an important device in rubber processing, plays a crucial role in the field of rubber extrusion molding due to its excellent performance and wide applicability. Compared with plastic melt gear pumps, rubber melt gear pumps have demonstrated strong adaptability to different types of rubber materials, head resistance, and operating conditions due to their unique working characteristics, thus winning a wide range of application space.
Rubber melt gear pumps have shown significant advantages in multiple processes such as precision extrusion molding, rubber filtration process, and rolling feeding. Its precise control ability and efficient conveying performance enable rubber materials to achieve more precise shaping and higher production efficiency during the processing. Therefore, rubber melt gear pumps have become an emerging hot spot in the international rubber and thermoplastic elastomer processing field, attracting widespread attention and research from industry insiders.
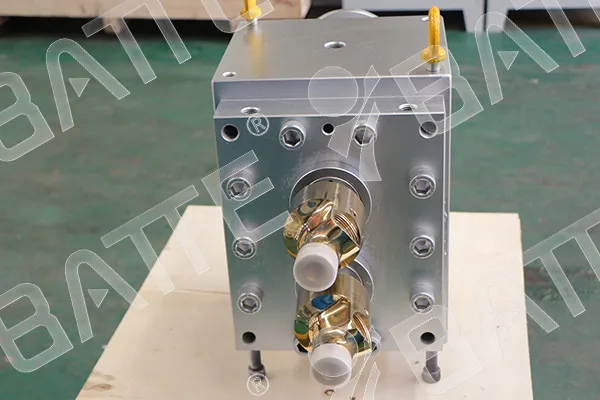
Related studies have shown that rubber gear pump extruders have a wide range of application scenarios in rubber processing. It can be used in multiple stages of rubber filtration, preheating, plasticization, and molding, providing stable and continuous material supply for rolling machines. In addition, rubber gear pump extruders can also be used in conjunction with hot feed extruders, cold feed extruders, and cold feed exhaust extruders to achieve composite extrusion, conveying, traction belts, flat products, rubber hoses, rubber strips, inner tubes, wires and cables, as well as extrusion molding of various rubber products and filling of rubber rollers and high-capacity molds.
In gear pumps, gears, as their key components, have a decisive impact on the performance of the pump. According to the tooth direction, gears mainly have three types: straight teeth, helical teeth, and herringbone teeth. Compared to spur gears, helical gears have a higher degree of meshing and can achieve continuous and stable material extrusion, reduce pressure fluctuations, and thus improve production efficiency. Meanwhile, the self-cleaning effect of the helical gear rotation can effectively maintain the cleanliness of the tooth root and prevent material deposition and decomposition. However, helical gears generate axial forces during operation, which may have a certain impact on the service life of bearings and exacerbate the shear effect of the melt in the tooth side clearance. Therefore, when designing helical gears, it is necessary to control the size of the bevel angle reasonably.
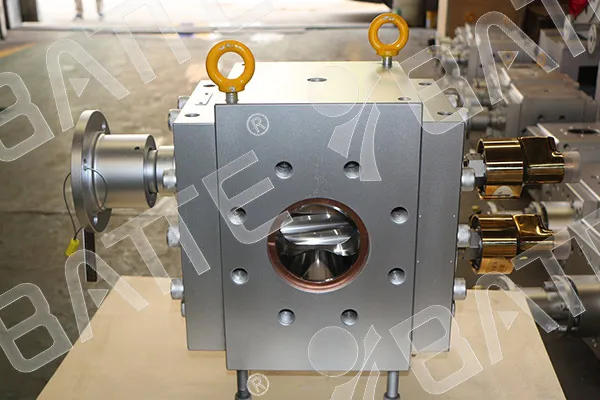
Straight gears have advantages such as balanced bearing load and lower processing costs. However, its disadvantage is also quite obvious, that is, the pressure fluctuation amplitude is large, which may have a certain impact on the quality of rubber products. The herringbone gear combines the advantages of helical and spur gears, achieving smooth extrusion and balancing axial force. However, herringbone gears are prone to material retention at the tooth root and have high processing costs, which to some extent limits their application range.
In summary, rubber melt gear pumps have broad application prospects and important research value in the field of rubber processing. By continuously optimizing gear design and improving process parameters, the performance and stability of rubber melt gear pumps can be further improved, providing strong support for high-precision and high-efficiency production of rubber products.
Email: info@battemachinery.com
WhatsApp: +86 158 38331071