What are the application scenarios of melt pipe pumps?
The application scenarios of melt pipe pumps are extremely versatile, primarily focused on the transportation, pressurization, and metering of high-temperature, high-viscosity polymer melts. The following outlines the specific application scenarios of melt pipe pumps:
I. Industrial Applications
1.Plastics, Resins, and Rubber Products Industry:
Extrusion Molding: In the extrusion process of products such as granules, films, pipes, sheets, plates, artificial fibers, optical fibers, and medical plastic catheters, melt pipe pumps are installed between the extruder outlet and the die head, performing functions of pressurization, pressure stabilization, and metering. This application significantly enhances the dimensional accuracy and quality of extruded products, reduces waste and rejects, and can increase production capacity and reduce energy consumption to a certain extent.
Compounding Extrusion Granulation: Combining a co-rotating twin-screw extruder with a melt pipe pump forms a compounding extrusion granulation line, which significantly improves the mixing quality and output compared to standalone twin-screw granulation units, while notably reducing energy consumption per kilogram of material processed.
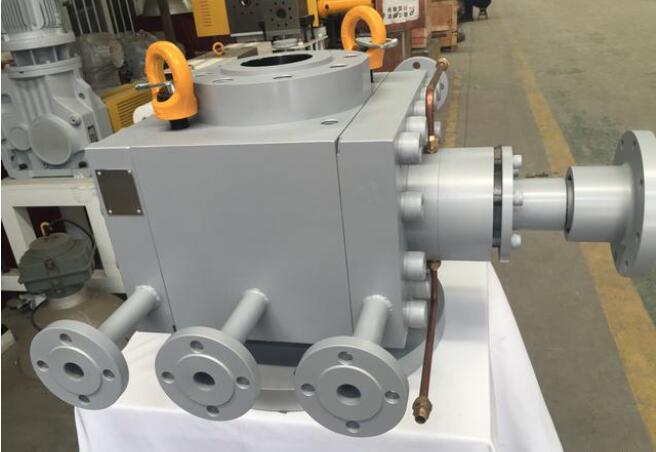
2.Chemical Fiber Industry:
In the production of chemical fiber products, melt pipe pumps are also used for the transportation, pressurization, and metering of high-temperature, high-viscosity polymer melts, ensuring process stability and product quality.
3.Other Polymer Material Industries:
For materials such as hot-melt adhesives, asphalt, paints, adhesives, pharmaceuticals, food, fats and oils, fuels, dyes, coatings, lubricants, and polyols that do not contain particulate impurities, melt pipe pumps play a crucial role in their transportation.
II. Specific Functions
Stable Pressure Output: Melt pipe pumps effectively mitigate material output instability and pressure pulsations caused by extruder parameters, ensuring smooth production processes.
Improved Product Quality: By minimizing dimensional tolerances of extruded products, reducing waste and rejects, and enhancing overall product quality.
Increased Extrusion Output: By transferring the decompression function from the extruder to the melt pipe pump, the extruder can operate at lower pressures and temperatures, improving extrusion efficiency while reducing melt residence time in the screw barrel, stabilizing the plasticization process, lowering melting temperatures, and thereby enhancing product output and quality.
Reduced Unit Energy Consumption: The application of melt pipe pumps reduces energy consumption during production, enhancing overall production efficiency.
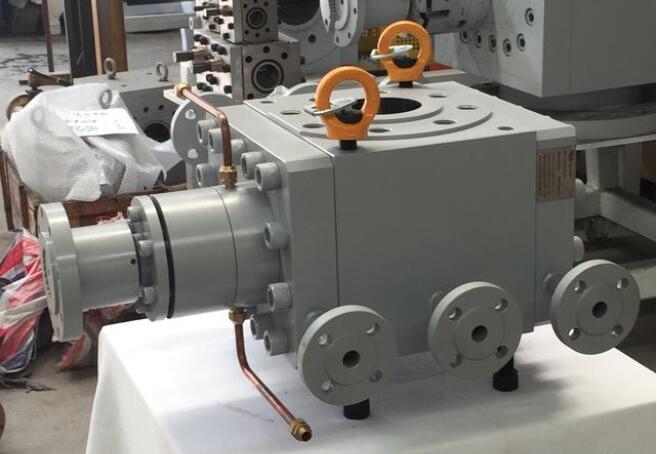
III. Technical Characteristics
Wear and Corrosion Resistance: Made from high-wear and corrosion-resistant high-temperature alloy steel materials, melt pipe pumps undergo a series of thermal processing and surface treatments, rendering them suitable for various complex operating conditions with their high temperature, high pressure, wear, and corrosion resistance.
Precise Metering: Melt pipe pumps possess precise metering capabilities, ensuring stable and accurate melt flow rates to meet high-precision production requirements.
Easy Maintenance: With a rational structural design, melt pipe pumps are easy to disassemble, clean, and maintain for routine upkeep.
In conclusion, thermoplastic melt pump are indispensable equipment in the plastics, resins, rubber, and chemical fiber industries due to their capabilities in stable pressure output, improved product quality, increased extrusion output, and reduced unit energy consumption.
Email: info@battemachinery.com
WhatsApp: +86 158 38331071