How to choose the melt pump for 800-1000kg/h plastic extruder
In selecting a melt pump for a plastic extruder with a capacity range of 800-1000kg/h, multiple factors need to be considered to ensure that the chosen pump meets production requirements while offering superior performance and stability. Below are some crucial steps and considerations for selection:
I. Clarify Production Requirements
Output Demand:
Confirm that the extruder's output range falls within 800-1000kg/h, which serves as the primary basis for selecting the melt pump.
Material Characteristics:
Understand the type (e.g., PP, PET, PVC, etc.), viscosity, and temperature characteristics of the plastic melt to be conveyed.
Pressure Requirements:
Determine the inlet and outlet pressure requirements of the melt pump, as well as the maximum pressure fluctuations that may be encountered during conveyance.

II. Consider Pump Performance Parameters
Flow Range:
Select a melt pump with a flow range that encompasses 800-1000kg/h to ensure production needs are met under various operating conditions.
Pressure Stability:
The melt pump should exhibit excellent pressure stability, capable of continuous operation under high temperature and pressure conditions with minimal outlet pressure fluctuations.
Temperature Resistance:
Choose a melt pump that can withstand temperatures corresponding to the plastic melt's requirements. Typically, the pump's operating temperature should exceed the maximum temperature of the plastic melt.
Wear Resistance:
Given the high viscosity of plastic melts, the melt pump must possess good wear resistance to prolong its service life.
Sealing Performance:
The sealing performance of the melt pump directly affects its operational stability and efficiency. Select a pump model with excellent sealing capabilities.
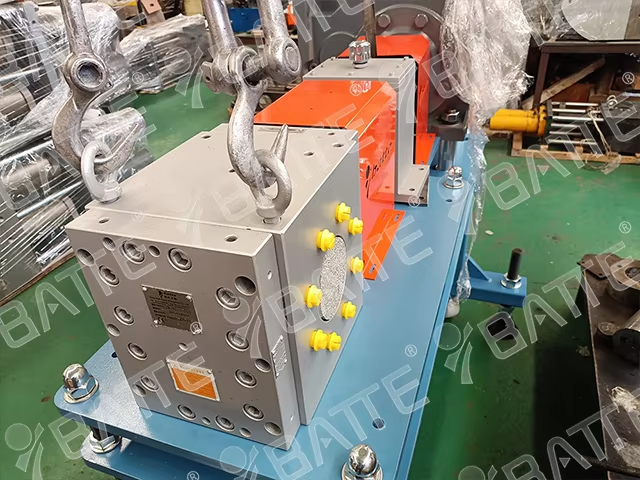
III. Focus on Pump Structure and Materials
Pump Body Structure:
The melt pump's structure should be compact and rational, facilitating installation and maintenance. Additionally, the pump's interior should be designed with reasonable flow channels to reduce resistance during melt conveyance.
Material Selection:
The primary components of the melt pump (e.g., pump body, gears, bearings) should be made of materials that are high-temperature resistant, wear-resistant, and corrosion-resistant. Common materials include alloy steel and high-temperature tool steel.
Email: info@battemachinery.com
WhatsApp: +86 158 38331071