Installation method of reactor kettle melt pump
The installation method of the reactor melt pump is primarily determined by specific application scenarios and process requirements, but it can generally be summarized into the following key steps and precautions:
I. Pre-installation Preparation
Equipment Inspection:
Before installation, carefully inspect the melt pump for any external damage and ensure all accessories are complete. Verify that the pump body, motor, reducer, and other components are undamaged and meet design specifications.
Determining Installation Location:
Determine the installation location of the melt pump based on process requirements. The location should facilitate easy operation and maintenance, taking into account factors such as the pump's inlet and outlet directions and height. Typically, the reactor melt pump is installed at the bottom of the reactor for direct extraction of the melt.
Preparing the Foundation:
Prepare a foundation according to the pump's requirements, ensuring it is level and stable. The foundation should be securely connected to the floor or frame to withstand the pump's operating load.
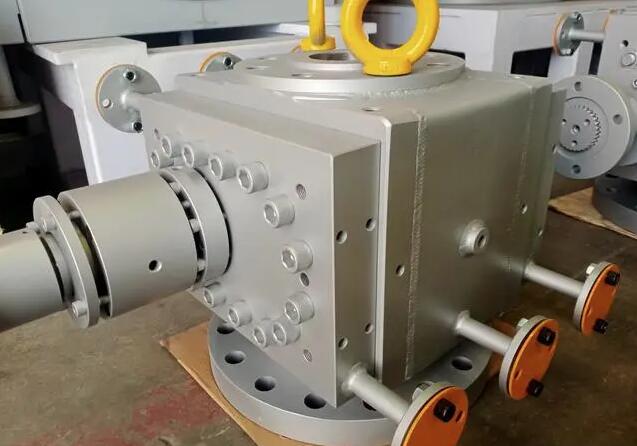
II. Installation Steps
Positioning the Pump:
Place the melt pump on the foundation, ensuring the pump axis aligns with the inlet and outlet pipe axes. Adjust the pump's height as needed to ensure smooth connection of the inlet and outlet pipes.
Installing the Motor and Reducer:
If using a motor + reducer + universal joint installation configuration, first mount the motor and reducer on the foundation, ensuring a secure and reliable connection between them. The universal joint provides compensation, balancing displacement caused by thermal expansion of the reactor and piping, ensuring smooth operation of the entire system.
Connecting Piping:
Securely connect the inlet pipe to the pump inlet. Keep the piping as straight as possible, avoiding bends and sharp turns to reduce resistance and wear. Install a filter at the inlet to prevent impurities and foreign objects from entering the pump. Similarly, securely connect the outlet pipe to the pump outlet, maintaining piping straightness. Install accessories such as pressure gauges and safety valves as needed to monitor the pump's operating status.
Installing Sealing Gaskets:
Install sealing gaskets between the inlet and outlet pipe flanges. Ensure the gaskets match the flanges and are flat and clean for optimal sealing.
Tightening Bolts:
Secure the inlet and outlet pipe flanges with bolts, applying even force during tightening to ensure uniform tightening and prevent leaks.
Electrical Connections:
Connect the pump's motor, sensors, and other components to the control cabinet or electrical control system according to the electrical schematic diagram, ensuring secure and correct connections.
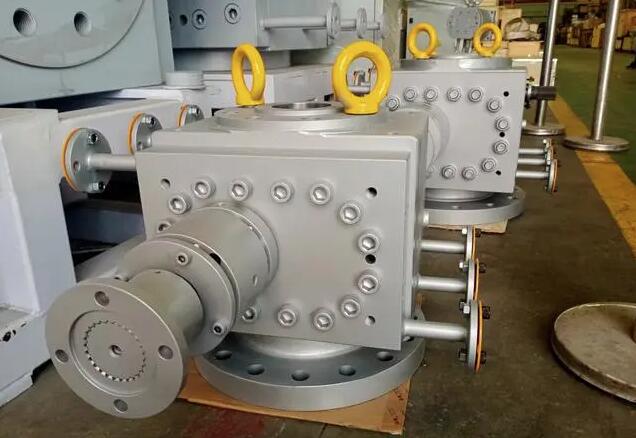
III. Debugging and Trial Run
Manual Turning:
Before starting the motor, manually turn the pump to check for any blockages or resistance.
Trial Run:
Start the motor for a trial run, checking the pump's rotation direction and sealing performance. Closely monitor the pump's operating status, checking for abnormal sounds or vibrations. Verify that inlet and outlet pressure and flow rate parameters meet requirements.
Adjustment and Optimization:
If any abnormalities are detected, promptly stop the pump, inspect, and troubleshoot. Based on the trial run results, make necessary adjustments and optimizations to the pump's installation and settings.
IV. Precautions
Protecting Equipment:
Handle and place the pump with care, avoiding violent shocks and impacts that could damage its exterior or internal components.
Stable Foundation:
Ensure the foundation is level and stable to withstand the pump's operating load.
Secure Piping Connections:
Pay attention to the security and sealing of piping connections to prevent leaks and potential safety hazards.
Electrical Safety:
Ensure electrical connections comply with relevant safety standards to maintain stable operation of the electrical system.
Maintenance and Servicing:
Follow the manufacturer's instructions for maintenance and servicing to extend the pump's lifespan and maintain its optimal performance.
Email: info@battemachinery.com
WhatsApp: +86 158 38331071