Melt pump and screen changer of single screw extruder
When selecting the melt pump and screen changer for a single-screw extruder, various factors must be taken into account to ensure that the chosen equipment meets production requirements and achieves optimal performance. Below is a detailed analysis of the selection process for both the melt pump and screen changer:
I. Selection of Melt Pump
The melt pump plays a crucial role in stabilizing flow, enhancing output, and improving product quality during the plastic extrusion process. For a single-screw extruder, selecting the appropriate melt pump is paramount.
Product Type and Material:
The type and material of the melt pump should be chosen based on specific operating conditions. For instance, the ZB-B series melt pump is suitable for applications with operating temperatures ≤400°C and outlet pressures ≤40MPa, while the ZB-H series can operate at higher temperatures and pressures (e.g., up to 510°C and ≤70MPa outlet pressure). In terms of materials, the ZB-B series employs chromium-nickel alloy steel and high-temperature tool steel, whereas the ZB-H series may utilize imported CPM tool steel or tantalum-titanium alloy materials, with overall quenching for high hardness and excellent wear resistance.
Performance Parameters:
Attention should be paid to the melt pump's flow rate, pressure, viscosity, and other performance parameters to ensure they meet the needs of the production line. Additionally, the heating method (e.g., electric heating rods or thermal media heating) and drive mode (e.g., motor + reducer + universal coupling + pump body) of the melt pump must be selected according to specific circumstances.
Application Effects:
The melt pump stabilizes pressure output, reducing material flow instability and pressure pulsation caused by extruder parameter fluctuations. It enhances product quality, decreases scrap and waste rates, enabling even ordinary extruders to produce high-precision products. Furthermore, it increases extrusion output, lowers unit energy consumption, and extends the extruder's service life.
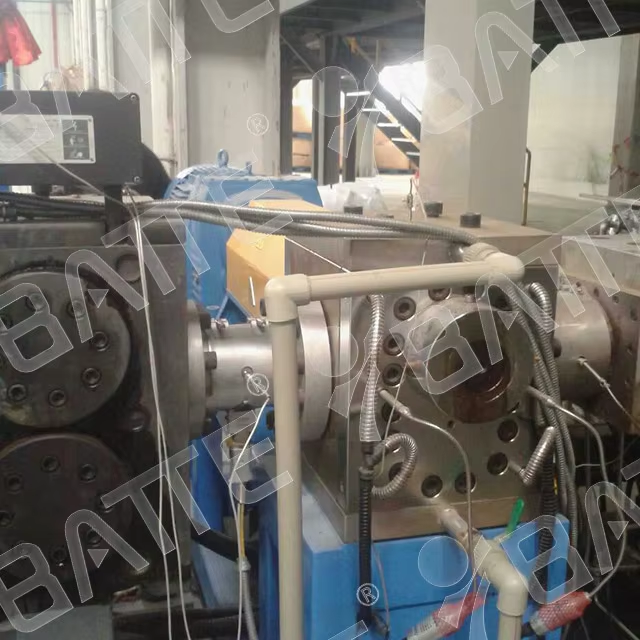
II. Selection of Screen Changer
The screen changer is used to replace filters during the plastic extrusion process, removing impurities from the melt to ensure product quality. For a single-screw extruder, selecting the right screen changer is equally important.
Material Properties:
Each material has unique melting points, melt flow indices, corrosiveness, and fluidity, which influence the requirements for the screen changer. Therefore, when selecting a screen changer, the material's characteristics must be thoroughly considered.
Production Requirements:
Different products have varying requirements for production continuity. For example, strand pelletizing necessitates uninterrupted strands, while producing cast film requires minimal pressure fluctuations during screen changes. Hence, the selection of a suitable screen changer must be based on actual production scenarios.
Extruder Type and Output:
Whether the extruder is single-screw or twin-screw, as well as its model, affects the choice of screen changer. Typically, the screen diameter should not be smaller than the screw diameter. Additionally, the extruder's output is a crucial factor in selecting a screen changer, requiring a suitable size to ensure production efficiency and product quality.
Pressure and Impurities:
The maximum pressure of the melt stream (in MPa) is also a significant consideration when selecting a screen changer. Overlooking this can lead to leakage or difficulty in operating the screen changer. When using recycled materials, the impurity ratio and the manufacturer's recommended filtration area must also be taken into account.
Type and Functionality:
Screen changers come in various types, such as hydraulic and plate-type screen changers. The selection should be based on actual needs and budget. Advanced screen changers with in-line screen changing capabilities can significantly enhance production efficiency and reduce downtime.
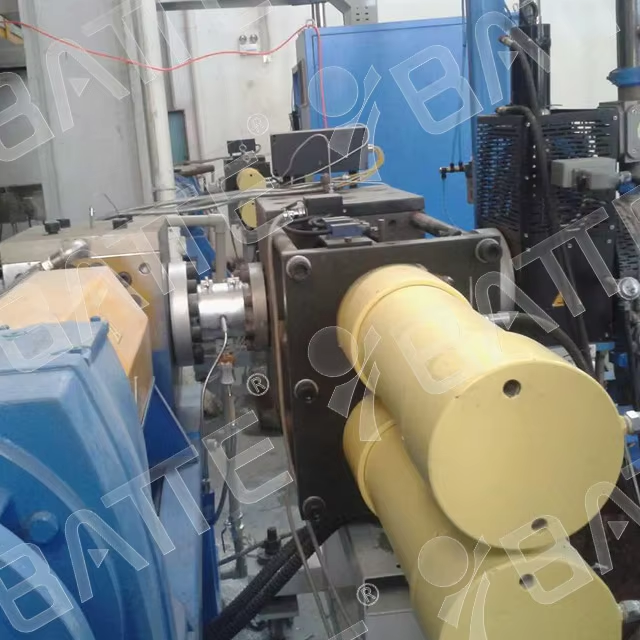
In conclusion, when selecting the melt pump and screen changer for a single-screw extruder, it is essential to comprehensively consider factors such as material properties, production requirements, extruder type and output, pressure and impurities, as well as equipment type and functionality. Additionally, specific analysis and selection based on individual circumstances are necessary to ensure that the chosen equipment meets production demands and achieves optimal performance.
Email: info@battemachinery.com
WhatsApp: +86 158 38331071