What are the functions of the melt pump control system?
The control system of the melt pump plays a crucial role in the operation and management of the melt pump, and its main functions can be summarized as follows:
Enhancing Output Stability of the Melt Pump:
The control system of the melt pump is capable of precisely regulating the pressure, temperature, flow rate, and rotational speed of the pump, effectively eliminating pressure fluctuations caused by factors such as uneven material feeding, temperature fluctuations in the barrel and die head, and pulsating screw speed. This stability is vital for improving the dimensional accuracy of extruded products and reducing waste rates, significantly enhancing product quality, especially in the extrusion industry.
Through intelligent algorithms and the analysis of extensive historical data, the control system can identify the optimal operating points for the melt pump under various media conditions, enabling efficient pump operation. This significantly shortens manual tuning time and reduces human and material costs.
Reducing Energy Consumption and Ensuring Production Continuity:
An excellent control system achieves better temperature control performance and drive power matching, thereby lowering energy consumption and production costs. By optimizing control parameters, it minimizes unnecessary energy losses and enhances energy utilization efficiency.
Moreover, the control system drastically reduces the frequency of manual intervention, increasing production efficiency and ensuring the continuity and stability of production. This is particularly crucial for large-scale, continuous production lines.
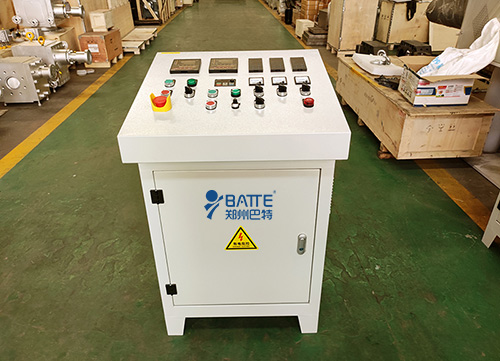
Providing Automation and Remote Control Capabilities:
The control system of the melt pump typically features a high degree of automation, enabling functions such as instrumentation control, PLC control, signal transmission, and remote monitoring. This remote control capability allows operators to monitor and operate tasks from a central control room, significantly improving their working environment and reducing the frequency and potential safety risks associated with on-site operations.
The remote control and monitoring functions also make the production process more flexible and efficient, enabling timely responses to production demands and market changes.
Improving the Working Environment for Operators:
The remote control function not only enhances production efficiency but also significantly improves the working environment for operators. In chemical equipment sites, where high temperatures, loud noises, and harmful gases are common, remote control prevents operators from being exposed to harsh environments for extended periods, protecting their health.
Safety Protection Mechanisms:
The control system typically incorporates various safety protection mechanisms, such as overload protection, overheat protection, and emergency stop, to ensure the safety of both the equipment and operators. These mechanisms promptly cut off power or halt operations when equipment malfunctions or abnormal situations arise, preventing further escalation.
Facilitating Maintenance and Fault Diagnosis:
The control system boasts a user-friendly interface and powerful diagnostic capabilities, simplifying routine maintenance and troubleshooting for operators. When equipment malfunctions, the control system can swiftly identify the issue and provide corresponding solutions or recommended measures.
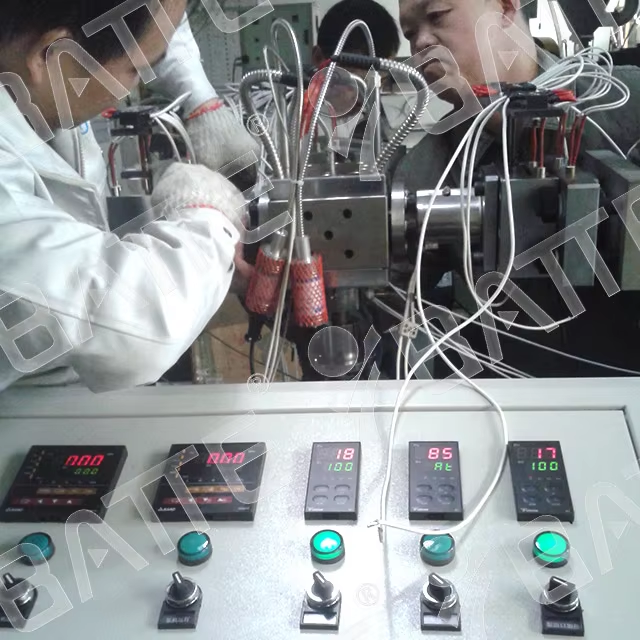
In conclusion, the control system of the melt pump plays a vital role in enhancing production stability, reducing energy consumption, providing automation and remote control capabilities, improving the working environment, and ensuring safety. It serves as a crucial safeguard for the stable operation and efficient production of the melt pump.
Email: info@battemachinery.com
WhatsApp: +86 158 38331071