What is the effect of melt pump speed on materials?
The influence of the rotational speed of a melt gear pump on materials is primarily manifested in the following aspects:
I. Material Flowability and Stability
Flowability: The rotational speed of the melt pump directly affects the flow velocity of the melt within the pipeline. Higher rotational speeds increase the flowability of the melt, enabling it to pass through pipes and molds more smoothly, which helps reduce clogging and stagnation. This is particularly crucial for materials requiring high flowability, such as certain low-viscosity or highly fluid plastic melts.
Stability: Appropriate rotational speeds maintain the stability of melt flow, preventing fluctuations or instability during transportation. This is vital for ensuring product quality and consistency. Excessively low rotational speeds may lead to impeded melt flow, while excessively high speeds may generate excessive shear forces, affecting the physical and chemical properties of the material.
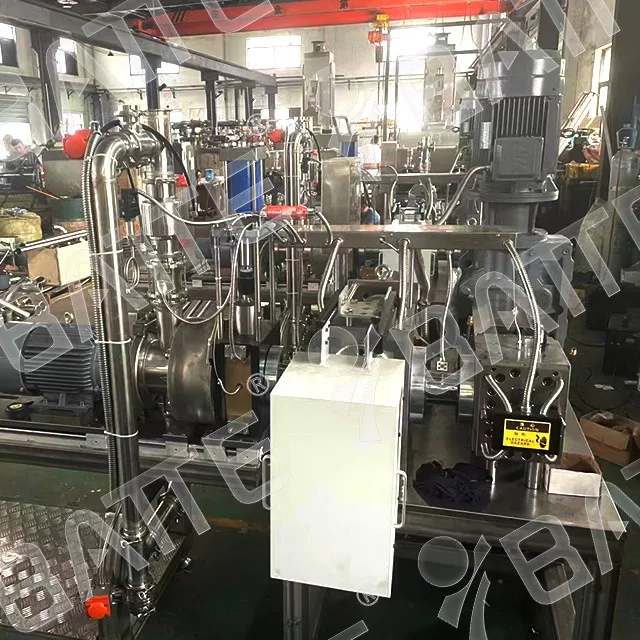
II. Material Quality and Appearance
Product Quality: The rotational speed of the melt pump must be selected and adjusted according to the quality requirements of the product. Suitable rotational speeds ensure that the melt maintains stable temperature, pressure, and flow rate during transportation, thereby avoiding defects or non-conforming products. For instance, in injection molding processes, an appropriate rotational speed ensures even filling of the mold, reducing defects such as bubbles and shrink holes.
Appearance Quality: The rotational speed of the melt pump also impacts the appearance quality of products. Excessively high rotational speeds may cause the melt to flow too quickly within the mold, resulting in flow lines or uneven surfaces. Conversely, excessively low speeds may allow the melt to remain in the mold for too long, leading to burning or discoloration of the product surface.
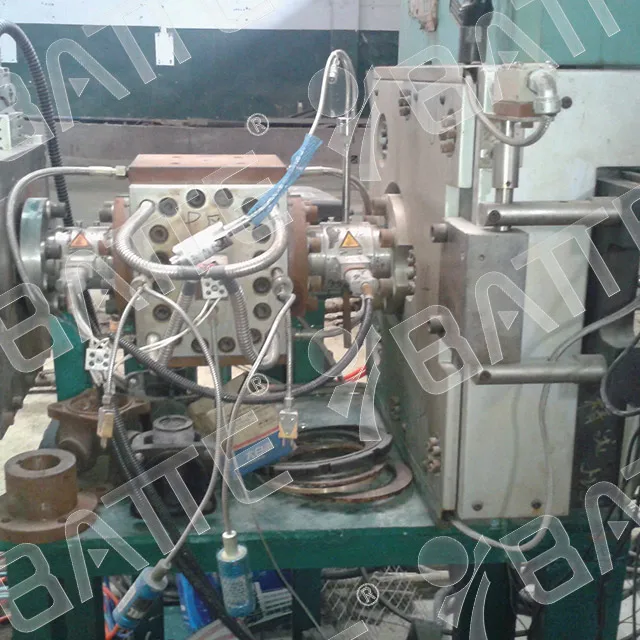
III. Production Efficiency and Energy Consumption
Production Efficiency: The rotational speed of the melt pump significantly affects production efficiency. Suitable rotational speeds ensure that the melt is transported to the mold at an appropriate speed, enhancing production efficiency and output. However, excessively high rotational speeds may cause overheating of the pump body, accelerated wear, and other issues, ultimately reducing production efficiency.
Energy Consumption: The rotational speed of the melt pump also influences equipment energy consumption. Under the premise of ensuring production efficiency, selecting lower rotational speeds can help reduce energy consumption and operating costs. Therefore, in practical applications, the choice of rotational speed must be comprehensively considered based on production needs and equipment performance.
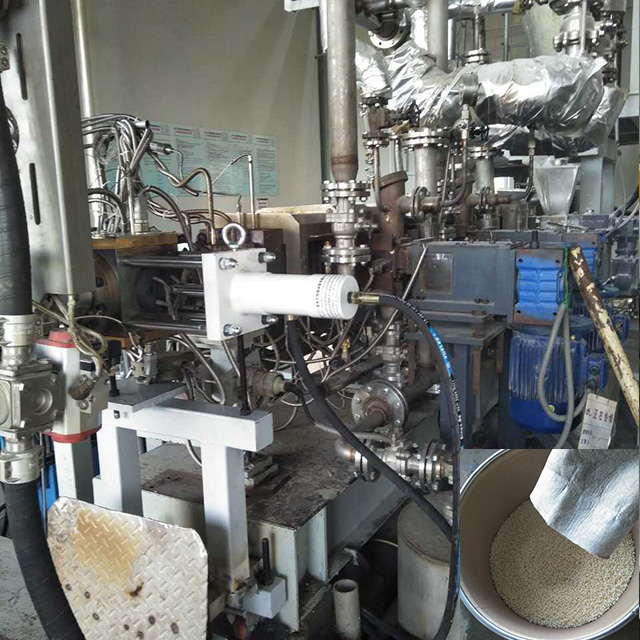
IV. Other Factors
Apart from the direct impacts mentioned above, the rotational speed of the melt pump may also be influenced by other factors, such as the viscosity, temperature, and pressure of the melt, as well as the design of the transportation pipeline. These factors interact, collectively influencing the performance of the melt pump and the effect of material transportation.
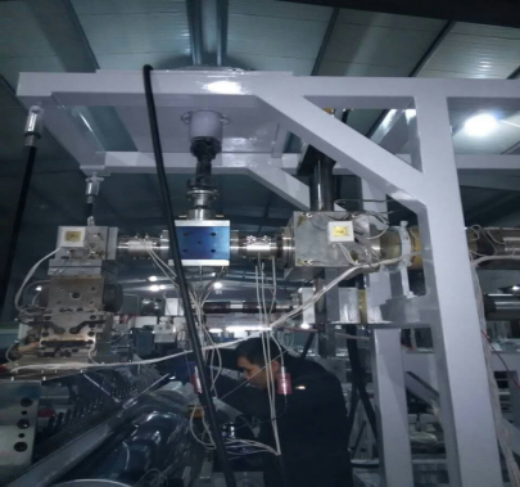
In summary, the rotational speed of the melt pump has multifaceted impacts on materials, necessitating reasonable selection and adjustment under the premise of ensuring product quality and production efficiency. In practical applications, comprehensive consideration and optimized design must be undertaken based on specific production processes and raw material characteristics.
Email: info@battemachinery.com
WhatsApp: +86 158 38331071