What are the applications of melt metering pumps in extruders
The application of melt metering pumps in extruders is mainly reflected in the following aspects:
I. Functional Roles
Stable Output Pressure: Melt metering pumps can significantly reduce the instability of material output and pressure pulsation caused by extruder parameters, ensuring a smooth extrusion process.
Improved Product Quality: By using melt metering pumps, the flow rate and pressure of molten materials can be precisely controlled, resulting in extruded products with small dimensional tolerances and high quality, effectively reducing waste and scrap rates.
Increased Extrusion Output: Melt metering pumps can reduce the pressure requirements on the screw. By building pressure towards the die head, the screw can extrude at high speeds, while reducing the residence time of the melt in the screw barrel, stabilizing the plasticization process, and increasing product output.
Energy Savings: The application of melt metering pumps can reduce the load on the extruder, conserve energy, and thereby reduce production costs. It is estimated that the use of melt metering pumps can reduce energy consumption by about 25% per kilogram of material processed.
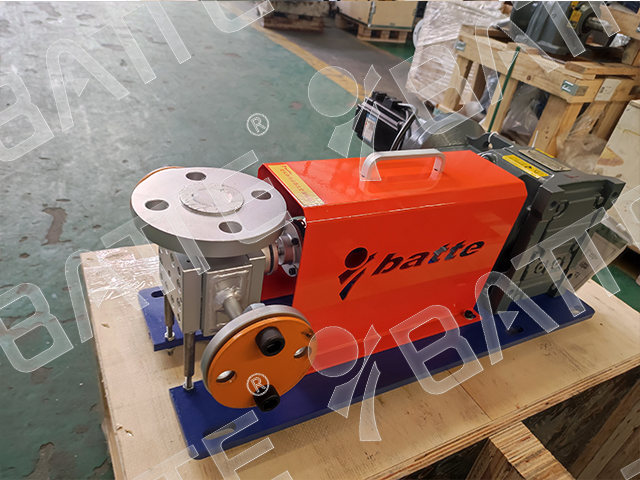
II. Working Principle
The working principle of melt metering pumps mainly relies on the rotational movement of their internal gears and the mutual engagement between the gears. When the gears rotate, the melt enters the tooth spaces of the two gears in the suction chamber. As the gears continue to rotate, the melt is brought into the discharge chamber from both sides. When the gears engage again, the melt in the tooth spaces is squeezed out of the discharge chamber and pressed into the outlet pipe. This process ensures stable delivery of the melt and high-pressure output.
III. Structural Characteristics
Melt metering pumps are typically composed of a pump body, front and rear side plates, two mutually engaged gears, bearings, and seals. The pump body is usually made of high-strength materials such as alloy tool steel to ensure reliability under high temperature and high pressure conditions. The gears and shafts are integrated to improve performance under high torque conditions. Additionally, the lubrication and sealing of melt metering pumps are relatively complex, often relying on the plastic melt being conveyed for self-lubrication to prevent contamination of the plastic melt.
IV. Application Scope
Melt metering pumps are mainly used for the conveying, pressurization, and metering of high-temperature, high-viscosity polymers such as plastics and rubbers. When the dimensional tolerances of extruded products are strictly required or the raw material costs are relatively high, the use of melt metering pumps becomes more necessary and valuable. Furthermore, melt metering pumps are widely used in various extrusion systems, such as sheet, plate, pipe, film, wire drawing, underwater pelletizing, masterbatch extrusion granulation, and rubber preforming.
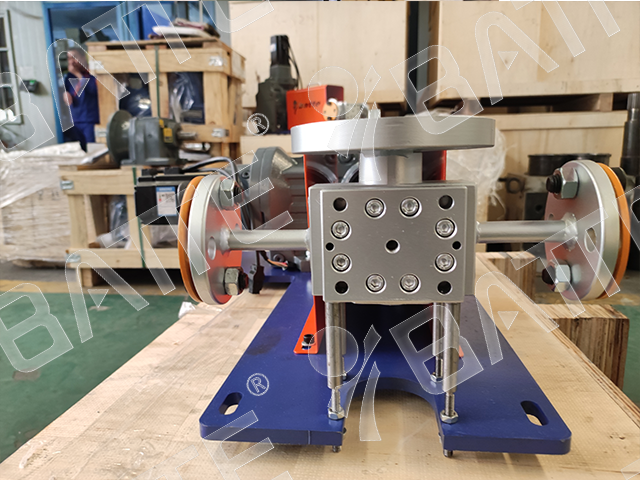
In summary, melt metering pumps have extensive application value in extruders, significantly improving the stability of the extrusion process and product quality, while reducing energy consumption and production costs.
Email: info@battemachinery.com
WhatsApp: +86 158 38331071