Applications of Melt Pumps in PP Yarn Woven Bag Production Li
The application of melt pumps in PP yarn woven bag production lines is not limited to the basic functions of conveying, pressure boosting, and pressure stabilization. They also play a crucial role in various aspects, as detailed in the following analysis:
Improving Dimensional Accuracy of Extruded Products
Melt pumps can eliminate feeding errors from the feeding system and significantly reduce fluctuations transmitted from upstream processes, enabling rapid stabilization of the working state. This stability minimizes the dimensional tolerance of extruded products, enhancing their dimensional accuracy. In the production of PP yarn woven bags, this means that the yarn strips will be more uniform and consistent in size, improving the overall product quality.
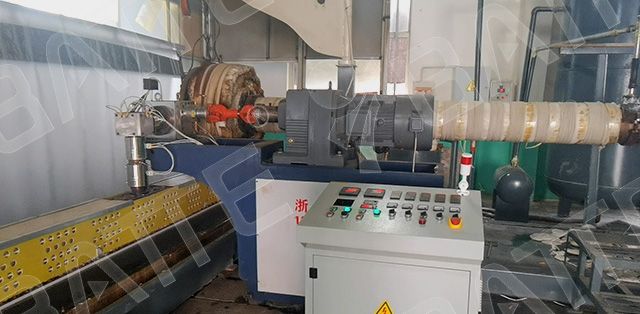
Simplifying Production Processes
In PP yarn woven bag production lines, melt pumps can be used in series with single-screw or co-rotating twin-screw extruders. This configuration eliminates the need for granulation and allows direct extrusion of products. This simplified production process shortens the production cycle and reduces energy consumption and production costs. For materials requiring blending and modification, this configuration offers significant advantages.
Reducing Wear on Screws and Barrels
The use of melt pumps reduces the pressure inside the extruder barrel, thereby minimizing wear between the screw and the barrel. This reduction in wear helps extend the service life of the extruder and reduces maintenance costs. In the production of PP yarn woven bags, this means that the production line can operate more stably, reducing downtime due to equipment failures.
Achieving Full-Process Online Monitoring and Feedback Control
Melt pumps exhibit linear extrusion characteristics, with their conveying capacity being basically linearly related to their rotational speed. This makes it easier to coordinate the operation of upstream and downstream equipment with the melt pump. By collecting information such as pressure and temperature at the inlet and outlet of the melt pump, full-process online monitoring and feedback control of the entire extrusion process can be achieved. This control capability helps detect and resolve production issues promptly, improving the stability and controllability of the production line.
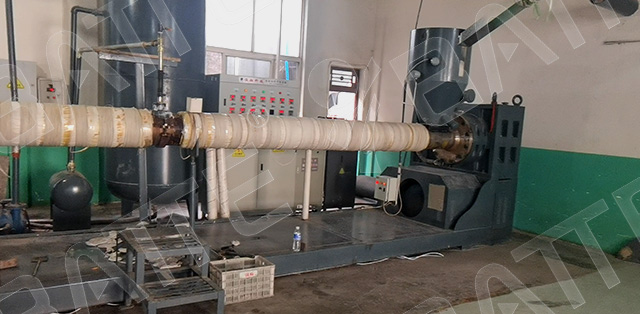
Enhancing Mixing Effectiveness
When melt pumps are used in combination with co-rotating twin-screw extruders, they can significantly improve mixing quality and output. This combination allows for more thorough mixing and shearing of materials during the extrusion process, enhancing the mixing effectiveness. In the production of PP yarn woven bags, this means that the bag materials will be more uniform and have more stable properties.
Enabling Low-Temperature Extrusion
Melt pumps can transfer the pressure-reducing function of the extruder to themselves, allowing the extruder to operate under lower pressure and temperature conditions. This low-temperature extrusion reduces energy consumption and helps maintain the stability of material properties. In the production of PP yarn woven bags, low-temperature extrusion helps reduce thermal degradation and oxidation of materials, thereby improving product quality and service life.
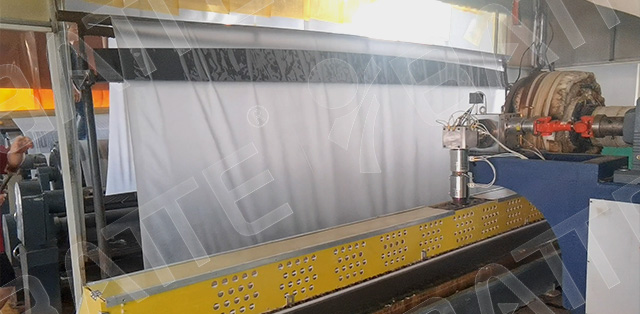
In summary, the application of melt pumps in PP yarn woven bag production lines offers various advantages. They not only improve product dimensional accuracy and overall quality but also simplify production processes, reduce energy consumption and production costs, extend equipment service life, achieve full-process online monitoring and feedback control, and enhance mixing effectiveness. These advantages make melt pumps an indispensable component in PP yarn woven bag production lines.
Email: info@battemachinery.com
WhatsApp: +86 158 38331071