Brief Description of the Advantages of Melt Pumps in Sheet Ex
Melt pumps offer numerous advantages in sheet extrusion machines, and the following provides a detailed introduction to these benefits:
I. Metering and Stable Extrusion
a. High-Precision Metering
Melt pumps can precisely control the flow rate of the melt. In the sheet extrusion process, there are high requirements for thickness uniformity. Through its precise gear structure, the melt pump can deliver the melt to the extrusion die at a very stable flow rate. For example, it can achieve a flow accuracy of ±1%, which means that during the extrusion of sheets, the amount of melt passing through the die per unit time remains almost constant, contributing to the production of sheet products with high thickness accuracy.
b. Stable Extrusion Pressure
Melt pumps can effectively eliminate pressure fluctuations generated by the upstream screw extruder. During the extrusion process, factors such as uneven material conveyance and minor changes in screw speed can cause pressure fluctuations in the screw extruder. The melt pump acts as a pressure stabilizing device, converting these fluctuating pressures into stable output pressures. It is like installing a pressure stabilizer in an unstable water pipeline, allowing the water to flow out at a stable pressure, thereby ensuring the continuity and smoothness of sheet extrusion, and reducing sheet thickness uniformity issues or surface quality problems caused by pressure fluctuations.

II. Improving Product Quality
a. Enhancing Sheet Quality
Due to its metering and stable extrusion capabilities, the melt pump has a significant effect on improving sheet quality. When extruding thinner sheets, such as plastic sheets for food packaging (with thicknesses ranging from 0.1 to 0.5mm), the melt pump can ensure uniform sheet thickness, avoiding local thicknesses that are too thick or too thin. Additionally, it can make the sheet surface smoother because a stable melt flow rate can reduce turbulence and irregular flow of the melt at the die, thereby lowering surface roughness and improving the product's appearance quality.
b. Improving Product Performance Consistency
For sheets with strict physical performance requirements, such as those used for electronic equipment insulation, consistency in performance is crucial. The stable extrusion of the melt pump ensures more uniform molecular orientation and crystallization within the sheet. The stable pressure and flow rate stabilize the cooling and molding processes of the melt during extrusion, resulting in sheets with better consistency in physical properties such as tensile strength and flexibility, ensuring the stability of product quality.
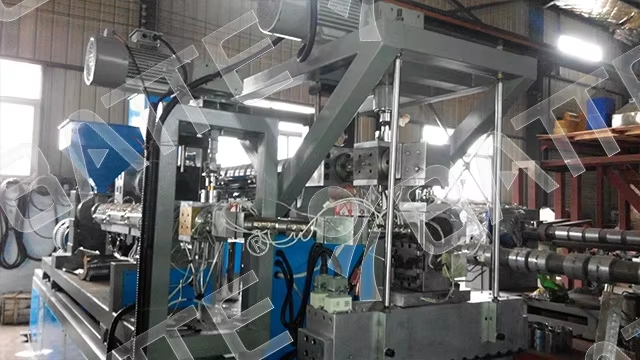
III. Production Efficiency and Cost Control
a. Increasing Production Speed
The melt pump allows the extruder to operate at higher speeds while ensuring product quality. Since it can stably convey the melt, it reduces the number of shutdowns due to quality issues (such as thickness unevenness requiring adjustments). For instance, without a melt pump, the extruder may only be able to operate at a lower speed to ensure product quality due to pressure fluctuations or unstable flow rates. However, with a melt pump installed, the extruder's production speed can increase by 30% - 50%, significantly improving sheet production efficiency.
b. Reducing Raw Material Waste
The metering function of the melt pump can reduce raw material waste. During the sheet extrusion process, without flow control, raw materials may be wasted due to excessive melt extrusion (resulting in sheets that are too thick and exceed standards). By controlling the flow rate, the melt pump ensures that the sheet thickness strictly meets requirements, reducing waste due to products not meeting specifications and lowering production costs.
Email: info@battemachinery.com
WhatsApp: +86 158 38331071