How to Install a Melt Pump on a Plastic Film Production Line?
Installing a melt pump on a plastic film production line requires following specific steps and precautions. Below is a detailed guide:
I. Preliminary Preparations
Determine Melt Pump Model:
Select the appropriate melt pump model based on the specific needs of the plastic film production line, such as the extruder model, production output requirements, and material characteristics.
Inspect the Installation Site:
Ensure the installation site is clean, dry, and well-ventilated. Verify that the foundation is flat and sturdy to prevent vibration or displacement during operation.
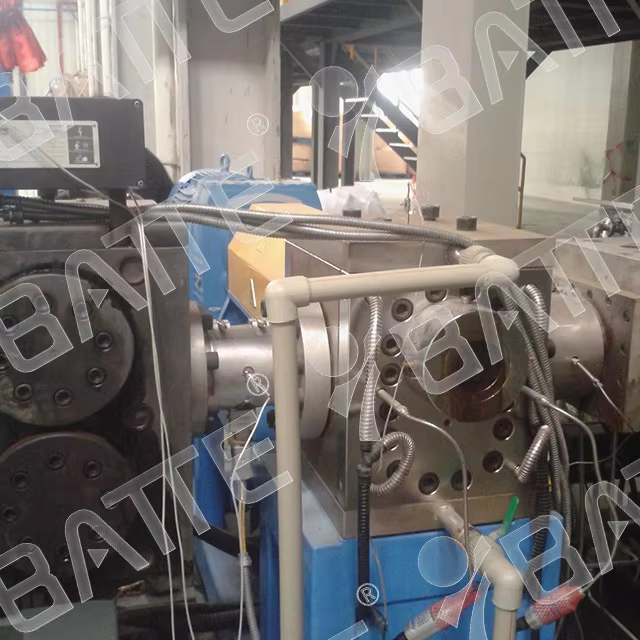
II. Installation Steps
Foundation Installation:
Place the foundation in the predetermined location according to the design drawings and adjust its levelness. Ensure the contact surface between the foundation and the ground is free of debris, and there is sufficient space around the foundation for subsequent installation work.
Pump Body Installation:
Position the melt pump body on the foundation, adjust its position and height, and ensure the pump shaft is horizontal. Secure the pump body to the foundation using bolts and ensure the connections are tight and leak-free.
Motor Installation:
Place the motor in the corresponding position and connect it to the pump body. Ensure the centerlines of the motor and pump body are aligned, and the motor base is securely connected to the foundation.
Seal Installation:
Select suitable seals according to equipment requirements. Install the seals onto the pump body and motor in the correct orientation, ensuring they are not twisted or damaged.
Piping Connection:
Connect the transfer piping to the inlet and outlet of the melt pump as needed. Ensure the connections are tight and leak-free, and consider piping support and fixation to prevent vibration or displacement.
Electrical Connection:
Connect the melt pump's motor, sensors, and other components to the control cabinet or electrical control system according to the electrical schematic diagram. Ensure connections are correct and secure to avoid electrical faults or safety hazards.
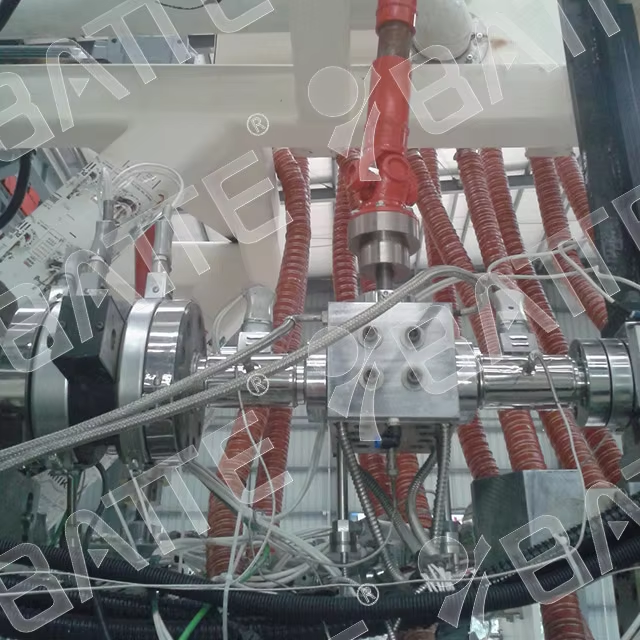
III. Commissioning and Trial Run
Commissioning:
After completing the installation steps, commission the melt pump. Check if the pump's rotation direction is correct and if the sealing performance is good.
Trial Run:
After commissioning, conduct a trial run. Check if the flow rate and pressure meet requirements, and listen for any abnormal sounds or vibrations. Adjust and repair issues promptly if found.
IV. Precautions
Safe Operation:
Strictly adhere to the equipment manual and operating procedures during installation and commissioning. Ensure installation quality and safety to avoid accidents.
Professional Installation:
For melt pumps with high precision and stringent requirements, it is recommended to have professionals handle installation and commissioning. This ensures equipment performance and accuracy, improving production efficiency.
Regular Maintenance:
Regularly maintain and service the melt pump, including checking the integrity of seals, cleaning the pump body and transmission components, and lubrication. Repair or replace damaged or worn parts promptly.
Monitor Status:
Monitor the melt pump's operating status, including flow rate, pressure, temperature, and other parameters. Address any abnormalities promptly to avoid affecting the production line's normal operation.
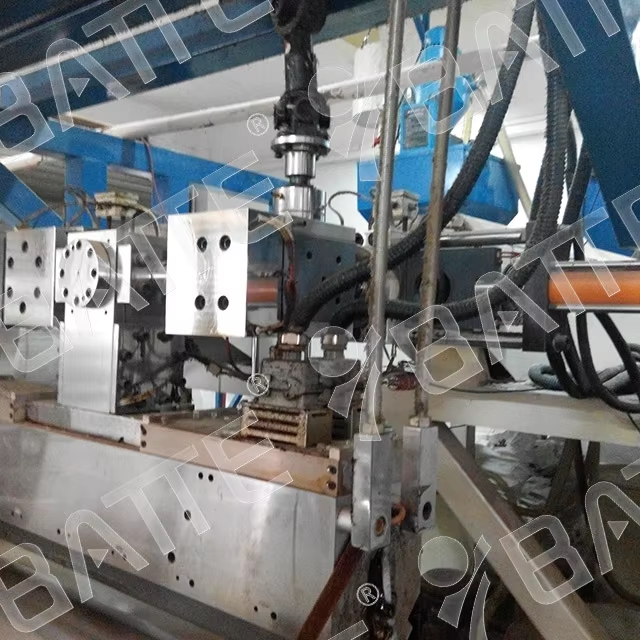
In summary, installing a melt pump on a plastic film production line requires following specific steps and precautions. Correct installation and commissioning, combined with regular maintenance and servicing, ensure the melt pump's stable operation and high efficiency, thereby improving the production efficiency and product quality of the plastic film production line.
Email: info@battemachinery.com
WhatsApp: +86 158 38331071