Thermoplastic Melt Pump: An Essential Component in Plastic Pr
In the vast field of plastic processing, thermoplastic melt pumps play a crucial role in ensuring the efficient and smooth flow of molten plastic material. These pumps are specifically designed to handle the high temperatures and pressures associated with melted thermoplastics, making them indispensable in various industrial applications.
What is a Thermoplastic Melt Pump?
A thermoplastic melt pump is a precision device used to convey and pressurize molten thermoplastics. It works by creating a continuous, steady flow of melted plastic material from one process stage to another. Unlike conventional pumps, which often struggle with the high viscosity and temperature of molten thermoplastics, melt pumps are engineered to handle these conditions with ease.
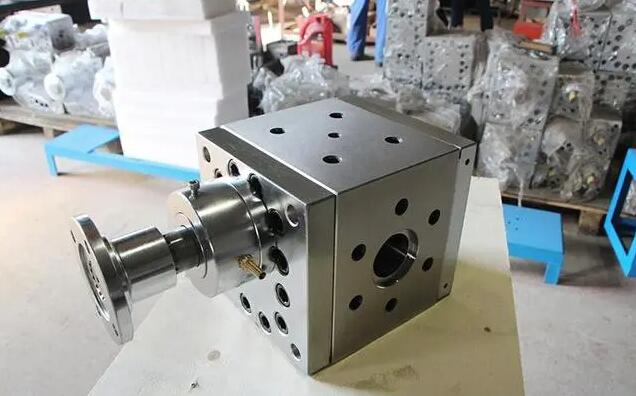
How Does a Thermoplastic Melt Pump Work?
Thermoplastic melt pumps typically operate under high pressure and at temperatures ranging from 200°C to 400°C, depending on the type of plastic being processed. The pump consists of a rotating screw or gear mechanism that engages with the molten plastic, pushing it forward through the pump body. This mechanism ensures that the plastic is uniformly pressurized and that any air bubbles or impurities are removed.
One of the key advantages of a melt pump is its ability to provide a precise and consistent flow rate. This is particularly important in processes such as extrusion, where variations in flow rate can lead to defects in the final product. Melt pumps also help to stabilize the pressure in the extrusion system, reducing the risk of surges and fluctuations that can damage equipment or compromise product quality.
Applications of Thermoplastic Melt Pumps
Thermoplastic melt pumps are widely used in a variety of plastic processing applications, including:
Extrusion: In extrusion processes, melt pumps are used to feed molten plastic into the extruder barrel at a controlled rate. This helps to ensure that the plastic is uniformly heated and mixed, resulting in a higher-quality final product.
Injection Molding: In injection molding, melt pumps are used to deliver molten plastic to the injection unit at a consistent pressure and flow rate. This helps to produce parts with precise dimensions and smooth surfaces.
Blow Molding: In blow molding, melt pumps are used to supply molten plastic to the parison head, where it is shaped into a hollow tube. This tube is then blown into the desired shape using compressed air.
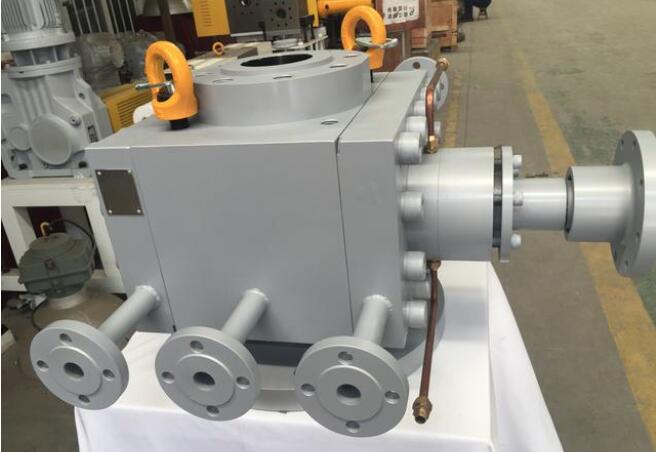
Benefits of Using Thermoplastic Melt Pumps
The use of thermoplastic melt pumps offers several benefits, including:
Improved Product Quality: By providing a consistent and precise flow rate, melt pumps help to produce plastic products with higher quality and fewer defects.
Increased Process Efficiency: Melt pumps can reduce the cycle time of plastic processing operations, leading to increased production rates and lower costs.
Enhanced Equipment Protection: By stabilizing the pressure in the extrusion system, melt pumps can help to protect against surges and fluctuations that can damage equipment.
Energy Savings: Melt pumps can reduce energy consumption by optimizing the flow of molten plastic, leading to lower operating costs.
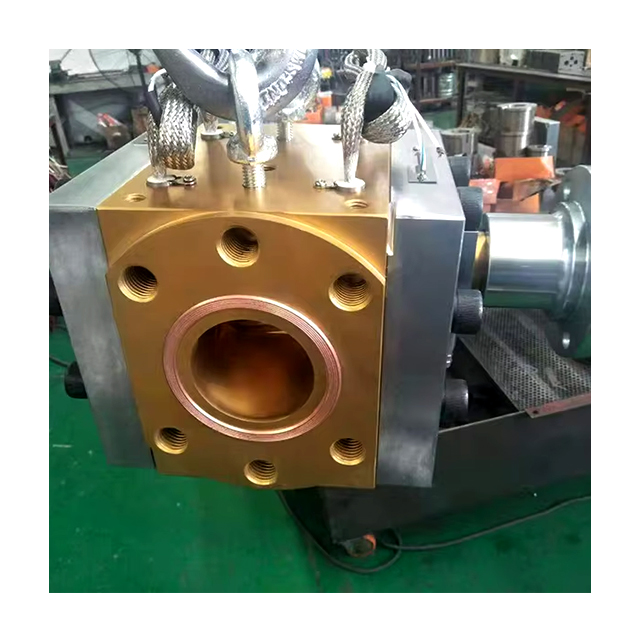
In conclusion, thermoplastic extrusion melt pumps are an essential component in plastic processing operations. Their ability to handle the high temperatures and pressures associated with molten thermoplastics, combined with their precision and reliability, makes them indispensable in a wide range of industrial applications. As the demand for high-quality plastic products continues to grow, the role of melt pumps in ensuring efficient and effective plastic processing will become even more important.
Email: info@battemachinery.com
WhatsApp: +86 158 38331071