Melt Pump for Plastic Film Extrusion: A Key Equipment in Plas
The melt pump for plastic film extrusion is critical equipment in the plastic film production process. Below is a detailed introduction covering its definition, working principle, functions, common types, and technological development trends.
I. Definition and Working Principle
Definition
The melt pump for plastic film extrusion (hereinafter referred to as the melt pump) is a positive displacement conveying device, primarily used to stably and uniformly deliver high-temperature molten plastics (such as polyethylene, polypropylene, etc.) to the extrusion die. Its core functions are to pressurize, stabilize pressure, and precisely meter the melt.
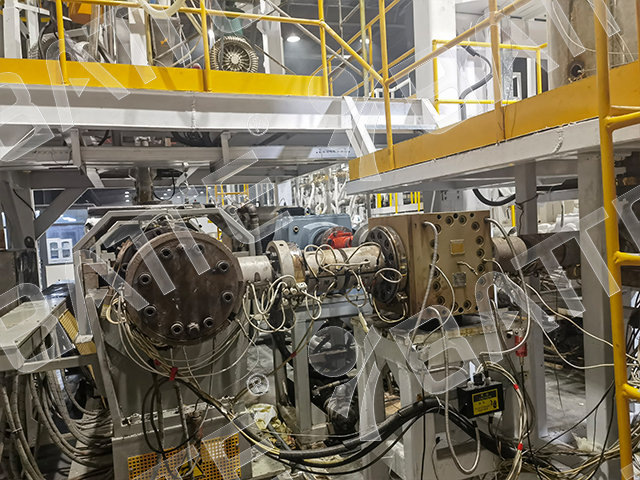
Working Principle
Structural Composition: Mainly consists of a pump body, driving gear, driven gear, bearings, seals, etc.
Conveying Process:
Suction Phase: Molten plastic enters the feed zone of the melt pump under the propulsion of the extruder.
Meshing and Conveying: As two precisely meshed gears rotate, the melt is enclosed in the chamber between the gear teeth and the pump body, moving towards the outlet as the gears rotate.
Discharge Phase: Gear meshing forces the melt out of the discharge zone and delivers it to the die head through the outlet pipeline.
Characteristics: The flow rate of the melt pump is strictly proportional to its rotational speed, and pressure fluctuations have minimal impact on its output, thus enabling high-precision metering.
II. Functions in Plastic Film Production
The melt pump is crucial for enhancing film quality and production efficiency, primarily manifested in the following aspects:
Stabilizing Pressure and Flow
Eliminating pressure fluctuations caused by factors such as screw speed variations and uneven feeding in the extruder, ensuring uniform film thickness and reducing surface defects (e.g., wrinkles, crystal points).
Improving Extrusion Precision
Minimizing dimensional tolerances of extruded products through precise gear meshing, suitable for high-precision films (e.g., optical films, capacitor films).
Enhancing Productivity and Efficiency
Allowing the extruder to operate under low pressure and temperature conditions, reducing screw load, while the melt pump's independent pressurization enables higher extrusion speeds, increasing overall productivity by 20%-40%.
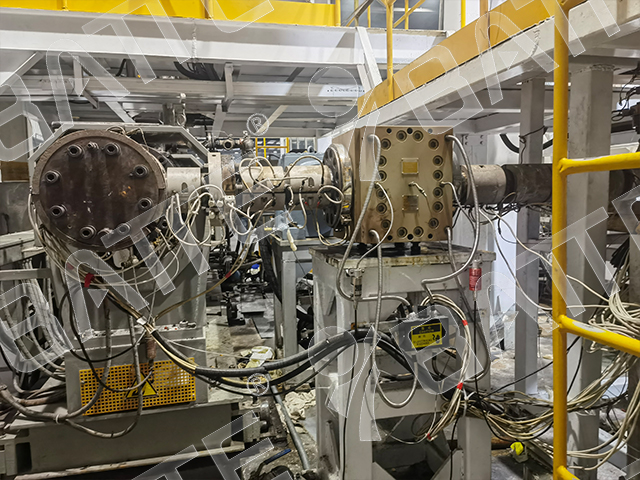
Optimizing Melt Quality
The shearing action of gears promotes dispersion of colorants and additives, resolving interfacial layering issues in multi-layer co-extrusion, and improving the mechanical properties and appearance consistency of the film.
Energy Saving and Consumption Reduction
Lowering the main motor load and reducing energy consumption by 10%-30%; stable processes reduce scrap rates and save raw material costs.
Extending Equipment Life
Reducing wear on extruder screws and barrels under low-pressure operating conditions, extending maintenance intervals, especially suitable for processing highly filled materials (e.g., glass fiber-reinforced plastics).
III. Common Types
Gear Pump (External Gear Type)
Features: Two identical meshing gears, simple structure, high metering accuracy, strong pressure resistance (up to 350Kg and above).
Applications: Widely used in PE, PP, and other film extrusion processes, suitable for high-viscosity melts.
Diaphragm Pump
Features: Utilizes compressed air or hydraulic drive to reciprocate diaphragms for melt conveying, with no leakage risk.
Applications: Suitable for special films with high hygiene requirements (e.g., medical packaging films).
Screw Pump
Features: Single or twin-screw structure, suitable for high-viscosity melts containing solid particles.
Applications: Used in film production involving the blending of filled masterbatches or recycled materials.
IV. Technological Development Trends
Intelligent Control
Equipped with frequency converters and online monitoring systems to achieve real-time feedback and automatic adjustment of pressure, temperature, and flow rate.
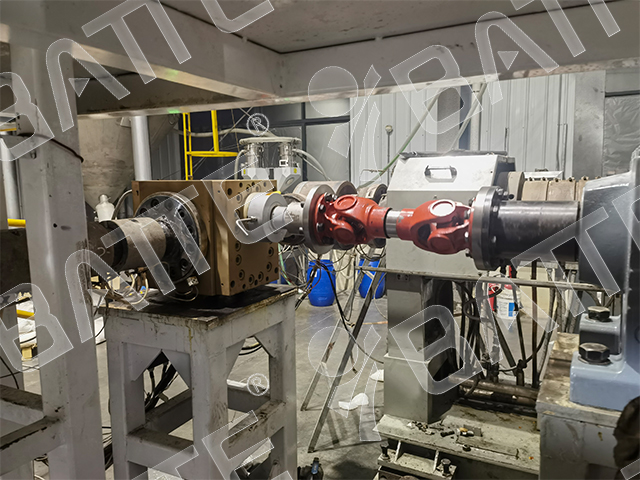
Material Upgrades
Employing high-temperature and corrosion-resistant alloy materials (e.g., Hastelloy) to adapt to higher processing temperatures (e.g., BOPP film production).
Modular Design
Supporting rapid model changes to adapt to production demands for films of varying thicknesses and widths.
Through its precise conveying mechanism, the melt pump for plastic film extrusion significantly enhances the stability, precision, and efficiency of film production. It is one of the core equipment in high-end film product (e.g., photovoltaic films, lithium-ion battery separators) production lines.
Email: sale@meltpump.com
WhatsApp: +86 158 38331071