Extrusion by thermoplastic melt pump
Extrusion by thermoplastic melt pump
Combining the very efficient plasticizing properties of screw and barrel configurations with the quantitative melt feed of thermoplastic melt pumps eliminates many of the negative effects. Extruders with excellent plasticizing properties are used to effectively masticate and feed the thermoplastic melt pump while using a pump to create higher die pressure without excessive temperature. In this configuration, the extruder and gear melt pump complement each other. When the screw for a good plastics work, but also lost its transmission efficiency. Conversely, when the gear melt pump highly effective delivery of plastic material will lose its plasticizing ability. For similarly sized extruders, the use of a gear melt pump to increase the pressure requires less for an extruder that can result in increased extrusion. The extruder is used only to obtain effective mastication and to ensure adequate throat feed to the gear pump.
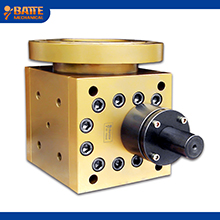
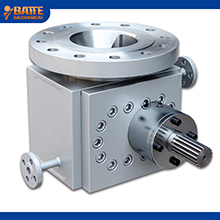
As a result, less energy is wasted due to pressure buildup, feeding the thermoplastic melt pump and the entire system will have to be increased. The advantage of extruding through a gear melt pump is that the extruder is "no-load" and the test results confirm that the extrusion amount pattern measured by the extruder-gear pump and the extrusion amount measured by the single-screw extruder similar. In other words, the combination of a 120mm extruder and a gear pump results in a similar amount of extrusion as a standalone 150mm extruder. Moreover, this amount of extrusion is linear because it is proportional to the pump speed, so it can be better controlled and has better predictability. Another significant advantage is that due to the quantitative feeding characteristics of the gear melt pump it is possible to adjust the pressure fluctuations of the system simultaneously and to reduce the pressure fluctuations by about 90%.
Constant and repeatable extrusion volume ensures constant head pressure so that extrusion uniformity is much better than typical extrusion processes. This is especially noticeable when considering the effects of changing feeding conditions. For example, changing a strip to sheet feed results in a significant weight change in less than a minute. As the gear melt pump with small friction on the rubber to move a small amount of rubber for indoor transmission of the transmission efficiency significantly improved (between 90% to 98%), so that the temperature of the pressure rise section significantly reduced rubber Scorch may also be reduced. According to the principle of quantitative flow gear pump for pumping energy efficiency up to 40%, the size of the decision by the pump structure, and single-screw extruder in the 15% to 25%. The dissipative energy of a thermoplastic melt pump with a rubber compound is certainly less than the dissipative energy in an extruder, which is why a gear pump is used to increase the pressure and the extruder is used to perform the plasticisation most effectively. Therefore, at the same backpressure, the temperature rise caused by the pressure increase in the gear melt pump is much lower, allowing the operation of the system to be carried out at a lower temperature. This also increases the amount of extruding because the thermoplastic melt pump extrusion speed is correspondingly higher before the temperature limit is reached.